Complete Cleaning and Filling Equipment for Container
and KEG’s
Capacity of the installation: 60 KEG’s per hour.
C l e a n o m a t CL 5
With four cleaning stations
one filling station
Capacity: 60 keg/h
S P E C I F I C A T I O N C L E A N O M A T CL 5
fully automatic, fully electronic KEG inside cleaning and filling machine (machine with lifting beam for different KEG-sizes 15 – 50 l KEG).
A fully automatic transport of Kegs with different height but same diameter is ensured without conversion of machine.
Execution:
The machine is made of a robust rectangular frame.
The cleaning- and filling station as well as
cylinders for lifting beam are installed in the
lower area of the machine.
The centering and storing table as well as lifting
beam are installed in the middle area.
Squeezing and pneumatic control are installed in
the upper area. The electric control can be
variably installed in the upper area of machine or
at the side of the machine in control cabinet. At
the side of machine in opposite to control side the
piping with all media valves which are connected by
the pipes with the different heads are installed.
material:
all steel parts used for fixed and movable parts
are made of stainless steel, mat. quality min.
1.4301/ AISI 304/18/8.
For slide bearings and wearing parts plastic
material Polyamide, coloured black, is used.
function:
The machine is operated from basic position. The basic position is indicated on the operation panel. If the machine is not in basic position or is in disturbance, the operation panel
shows the cause for the disturbance as well as necessary steps for elimination of disturbance.
Each single KEG is carried over locking device to the station. The Keg is centered on the centering station, taken over by the lifting bar and set on first cleaning head. The fitting of Keg is covered on cleaning head seal by squeezing. The slide opens the KEG fitting and the cleaning programme runs fully automatic by electrical control, pneumatic control and the media valves. At the same time the next Keg is taken over and pre-centered. The beer filling is controlled by differential pressure where start filling is slow and final filling can be effected fast and slow. It is possible to install volumetric flow measurement at any time without conversion of machine.
Disturbances and their causes are indicated on operation panel. The cleaning steps are monitored by liquid sensor, pressure sensor and temperature sensor. The stated cleaning times in cleaning programme are theoretical times.
pneum. control:
The control consists of cylinder, valves, fittings and tubes. The
pneumatic is the connection between electronic and operating cylinders. The pneumatic is clearly arranged in water protected stainless steel housing.
media control:
the valves are operated electro pneumatically and open or close
the media flow (cleaning agent, air, steam) from piping to head
and back. The valves are installed in the central piping in a way
to keep the way from valve to head and back short. The
advantage is, that many steps can be operated and fixed
components like germ rests are completely washed out of the
Keg.
necess. media:
mixed water: ca. 3,0-4,0 bar – 75 – 90 ° C
hot water: ca. 3,0-4,0 bar – 80 – 95 ° C
cleaning agent: ca. 3,0-4,0 bar – 80 – 05 ° C
beer: ca. 2,0-3,0 bar – -1 -+12 ° C
steam: ca. 2,5-3,0 bar -130 -140 ° C
CO2: ca. 2,5-3,0 bar
sterile air: ca. 2,5-3,0 bar
control air:ca. 5,0-6,0 bar
KEG sizes:
Kegs in nearly all different sizes can be handled with our machine. For automatic procedure it is necessary that following measures are kept.
KEG – diameter: min. 250 mm
KEG – Diameter.: max. 450 mm
KEG – height min.: 250 mm
KEG – height max.: 650 mm
The cleaning times on the active stations are variable. They will be agreed with customer and can be changed at any time on the operation panel. The Kegs will be cleaned very careful. You can operate additionally four different programmes.
A. washing only
B. steam filling head
C. clean beer line
D. clean filling head
The beer filling is effected by differential pressure where first filling is effected slow and final filling is effected fast.
The frame and all fixed and movable parts are made of stainless steel, Quality min. 1.4301/AISI 304/18/8.
Utility Tanks (CIP)
Recovery water
Detergent
Acid
Hot Water
Roller Conveyor with drive
As inlet-conveyor
and one lock
length 2,5 m
Roller Conveyor with drive
As outlet-conveyor
length 2,5 m
equipped with Water Blowing System for cleaning Kegs
Filters
For sterile air
For CO²
For steam
Keg-Turning Table
for turning filled kegs
Date Printer
With robust stainless steel control cabinet
Protection IP 65
Automatic cleaning of print head
Piping system for the Installation
including fittings, union etc.
Installation and commissioning of the system
Installation, commissioning and training
Of the operation personnel
Our machine includes:
Complete and comfortable control of the machine Siemens S7 300
all values and processes can be monitored
our reliable and tested alternating flow vent system (cleaning through feed pipe and fittings);
all machinery piping;
all indications in clear text, all temperatures and pressure can be set at the control panel
fully-automatic CIP-cleaning of the filling system; with timer for operation in the night
three integrated cleaning and filling programmes which can be set at the control panel
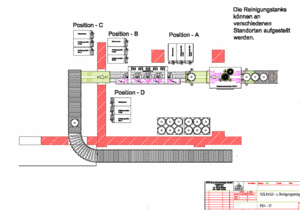